How Innovation is Transforming Building Construction
The building construction industry is undergoing a seismic transformation, driven by innovative technologies and new methodologies that challenge long-standing traditions and practices. The advent of standardized or prefabricated buildings, 3D printing and other groundbreaking technology based approaches has redefined how we think about time, cost and efficiency in building construction. These advancements are not just incremental improvements, rather they represent a paradigm shift that are changing the face of the built environment.
For centuries, the traditional method of construction has relied heavily on on-site labour, bespoke designs and manual processes. While this approach offers unparalleled customization and architectural freedom, it comes with significant downsides. Traditional construction is notoriously time-intensive, often taking many months or even years to complete a single project. This timeline is exacerbated by weather dependencies, labour shortages and unforeseen site complications. Additionally, the cost of traditional building methods can be prohibitive, driven by high labour expenses, labour shortages, material waste and project overruns.
In contrast, modern construction techniques such as prefabrication and 3D printing offer compelling advantages. Prefabrication involves manufacturing building components in a controlled factory environment before transporting them to the construction site for final assembly. This method significantly reduces construction timelines, often by as much as 50% compared to traditional methods. In addition, prefabrication is independent of weather variability, minimizes material waste, enhances quality control and reduces the environmental footprint of construction projects. It also provides cost savings by optimizing labour efficiency and streamlining timing and logistics.
3D printing takes the concept of efficiency to another level, leveraging advanced robotics and material science to “print” entire structures layer by layer. The technology has proven capable of producing houses in as little as 24 to 48 hours, a stark contrast to the months required for traditional builds. Moreover, 3D printing enables the use of innovative designs and materials such as recycled plastics and sustainable concrete alternatives, further aligning with global sustainability goals. The price point for 3D-printed homes is equally impressive, with some prototypes costing under $10,000 to produce, making affordable housing a tangible reality.

Despite the promise of these technologies, challenges remain. Prefabrication and 3D printing require a significant upfront investment in technology and infrastructure. They also demand a rethinking of design philosophies, as not all architectural styles or projects are suitable for these methods. However, the long-term benefits often outweigh the initial hurdles, particularly when viewed through the lens of scalability, sustainability and global housing demands.
NXT TEC. Ltd is a notable example of a company that is not only embracing these innovations but is also redefining what is possible in modern construction. Based in Australia, NXT TEC. specializes in developing advanced building technologies that prioritize speed, quality, cost efficiency and environmental sustainability. Their proprietary NXT® Building System exemplifies this ethos, offering a comprehensive approach to construction focusing on a building’s superstructure from the foundation to complete build and integrates prefabrication, sustainable materials and efficent design to optimize productivity for scalable projects.
The NXT®Building System enables entire structures to be assembled rapidly, with some projects completed in just weeks rather than months. For instance, an NXT® residence was constructed from slab to lock-up in just four days, reaching practical completion in only 5 weeks including fitout and landscaping. The system reduces the reliance on skilled on-site labour, addressing one of the most pressing issues in the construction industry—a chronic skilled labour shortage. Moreover, the system’s design flexibility allows it to accommodate various building types, from residential homes to commercial complexes, without compromising on quality or aesthetics.
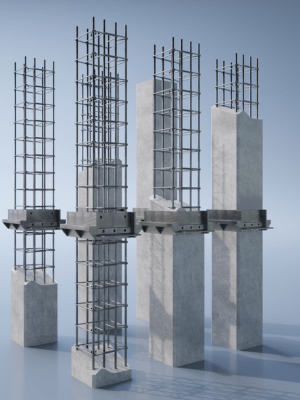
One of the standout features of NXT TEC.’s approach is its commitment to sustainability. The company’s building system uses materials that are not only durable but also environmentally friendly, aligning with the increasing demand for green construction practices. Additionally, the system minimizes waste during both the manufacturing and assembly phases, contributing to a more circular economy. This focus on sustainability is particularly critical as the construction industry accounts for a significant portion of global carbon emissions.
NXT TEC. has demonstrated the efficacy of its technologies through several high-profile projects. These case studies showcase how the company’s innovations translate into real-world benefits, from cost savings and reduced timelines to improved energy efficiency with homes achieving NatHERS 7+ star energy ratings and occupant satisfaction. By addressing both the immediate and long-term needs of developers and end-users, NXT TEC. is setting a new benchmark for the industry.
When comparing the cost dynamics of traditional construction versus modern methods, the differences are striking. Traditional builds often incur costs ranging from $1,500 to $3,000 per square meter, depending on the complexity and location of the project. Prefabricated constructions typically lower this range to between $1,200 and $2,000 per square meter, thanks to efficiencies in material usage and labour. Meanwhile, 3D printing offers the potential for even greater savings, with some projects coming in at less than $1,000 per square meter. NXT TEC.’s systems further enhance these savings by combining the best attributes of prefabrication and sustainable design, offering a compelling value proposition for developers and investors alike.
Time, of course, is another critical factor. While traditional construction timelines can extend well beyond a year for large-scale projects, prefabrication and 3D printing can compress this to a matter of weeks or months. This accelerated timeline not only reduces holding costs for developers but also allows for faster revenue generation. For example, a residential development using NXT TEC’s system can be completed and occupied in a fraction of the time it would take using conventional methods, enabling quicker returns on investment.
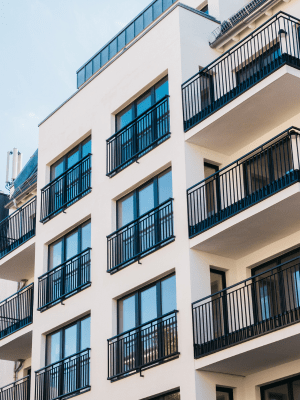
The societal implications of these advancements cannot be overstated. With global urbanization on the rise and housing shortages becoming increasingly acute, the ability to build quickly and affordably is more critical than ever. Prefabrication and 3D printing offer scalable solutions to these challenges, providing a pathway to address the housing needs of a growing population. Companies like NXT TEC. are proving that it is possible to meet these demands without sacrificing quality or the environment, making them invaluable players in the quest for equitable and efficient urban development.
In conclusion, the construction industry stands on the cusp of a transformative era. The shift from traditional methods to modern technologies such as prefabrication and 3D printing is reshaping the landscape, offering unparalleled advantages in terms of time, cost and environmental impact. NXT TEC. exemplifies how innovation can drive meaningful change, setting new standards for what is achievable in construction.
As the industry continues to evolve, the adoption of these methods will not only redefine how buildings are made but also who can access them, paving the way for a more sustainable and inclusive future.
PrimaryMarkets
PrimaryMarkets is a flexible and evolving Platform that responds in real time to the ever-changing investment environment. The Platform provides the infrastructure that enables shareholders in private companies to seek liquidity and in doing so it provides sophisticated investors with access to companies that are shaping the future in a wide variety of industries and sectors. We provide access to opportunities previously only accessible to institutional investors.
PrimaryMarkets exemplifies how innovation can transform the way we invest, trade and raise capital by breaking down traditional barriers, providing liquidity solutions and promoting transparency.
As the Platform continues to grow and evolve, it promises to unlock even more opportunities for investors and companies shaping the future of economies.